Steel Casting Cost Factors
5FFactors influencing steel casting parts price
1-Geometry and shape of part
Internal cavities, quantity and thickness of cores, thin walls, long parts, complicated shapes, more than one parting line requirement, non linear parting lines, reverse angles and nonsymmetrical parts and similar limitation will increase sand casting prices.
Mentioned complexities will increase casting defects such as cold lap, core replacement, flash, mismatch, raised core, deformation and other usual casting defects in result scrap rate will be higher than normal for these kind of parts.
2-Alloy and alloying elements
Alloying element according to their effects and induced properties are used in steel. The alloying elements in order of value increment are silicon, manganese, Chromium, Titanium, molybdenum, nickel, niobium and vanadium.
Although manufacturers should spend more for melt treatment and production of low carbon and special alloys.
The alloying element quantity and closed range of standards will also increase the prices.
3-Order quantity
Order quantity is effective in gating and risering design, molding material and process, pattern making costs.
4-Required Mechanical properties and heat treatment
Steels are heat treatable. Changing heat treatment process will change microstructure and mechanical properties of parts. Annealing and normalizing are usual heat treatment of steel parts that are used to homogenizing microstructure and decreasing solidification stresses.
In some cases to achieve required properties, multiple and costly heat treatments are used. For example normalizing, quenching and tempering are necessary in hardening cast steels. Depreciation of tools and furnaces in high temperature and related costs will increase the part price.
5-Requested tests according to safety and critical application
Safety and critical parts should produce under controlled processes and need more tests and qualifications. These kinds of tests are costly and will increase the prices.
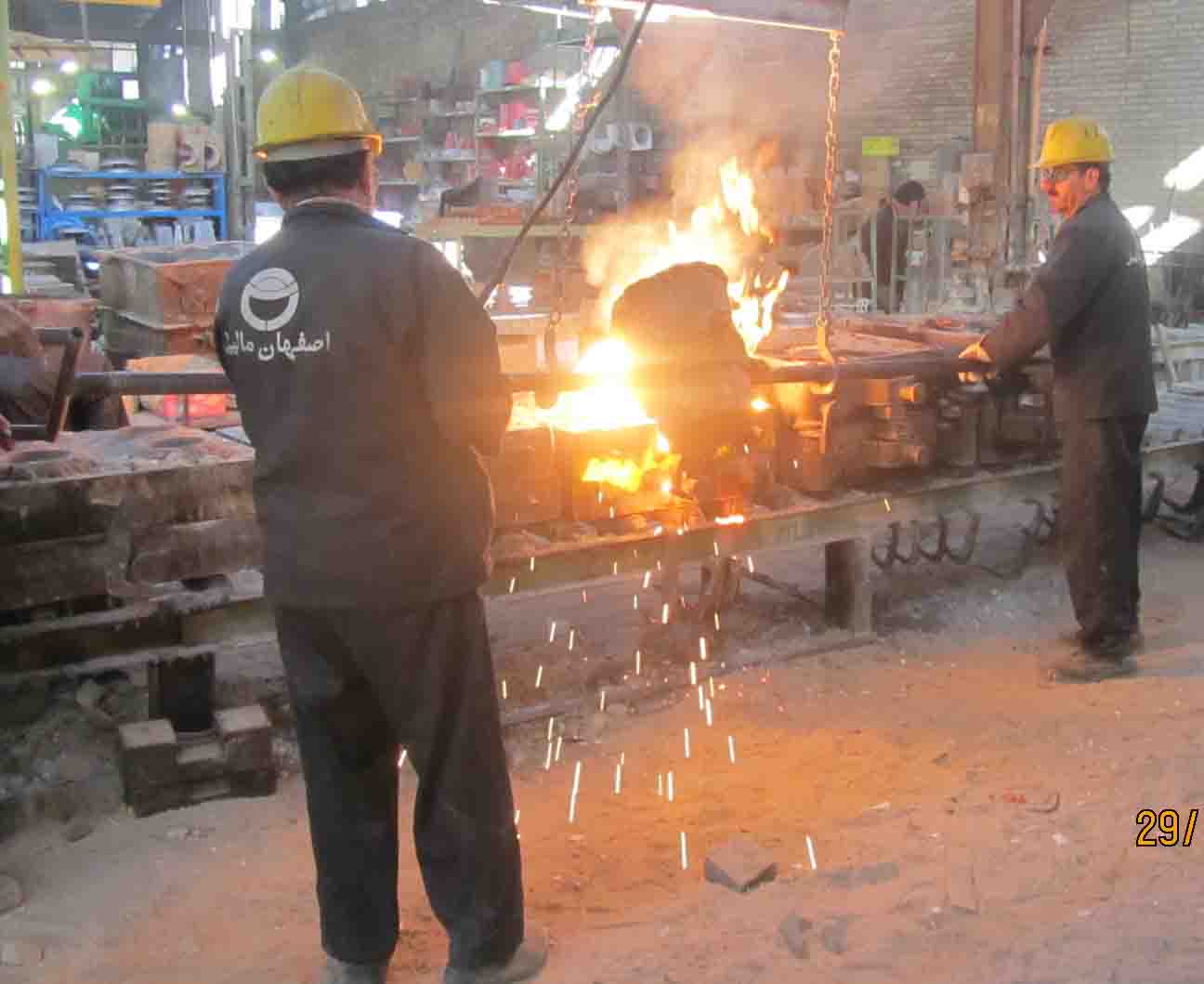